Magna ECS hosted a three-day conference in Linz from May 9th to May 11th, 2023, dedicated to the latest advancements in dynamic simulations and durability. Although I could only attend for half a day, I made sure to attend the Wednesday afternoon session. My colleague and I traveled from Herzograd to Voestahlstrasse in Linz, taking a train to the Ebelsberg station and then a city tram to the conference venue.
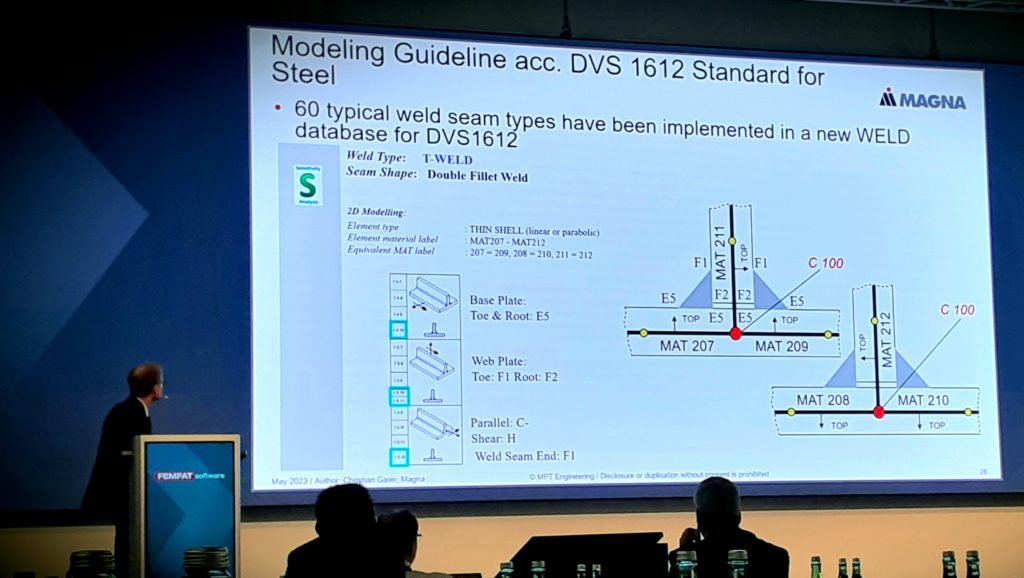
The first presentation (by Dr. Christian Gaier, Magna Powertrain Engineering Center Steyr) I attended focused on the latest features of FEMFAT 2023, Magna’s specialized software for durability and fatigue analysis. With its advanced post-processing capabilities, FEMFAT uses FEM results from other softwares to calculate safety factors and remaining life of mechanical components. The software also incorporates FKM guidelines and other relevant methods for precise results, making it an invaluable tool for calculating the strength of weld seams and composite materials.
The conference also featured discussions on the impressive achievements and potential applications of FEMFAT, as well as dynamic simulations. It was an enlightening experience to witness the latest developments in these fields and to be a part of this significant conference.
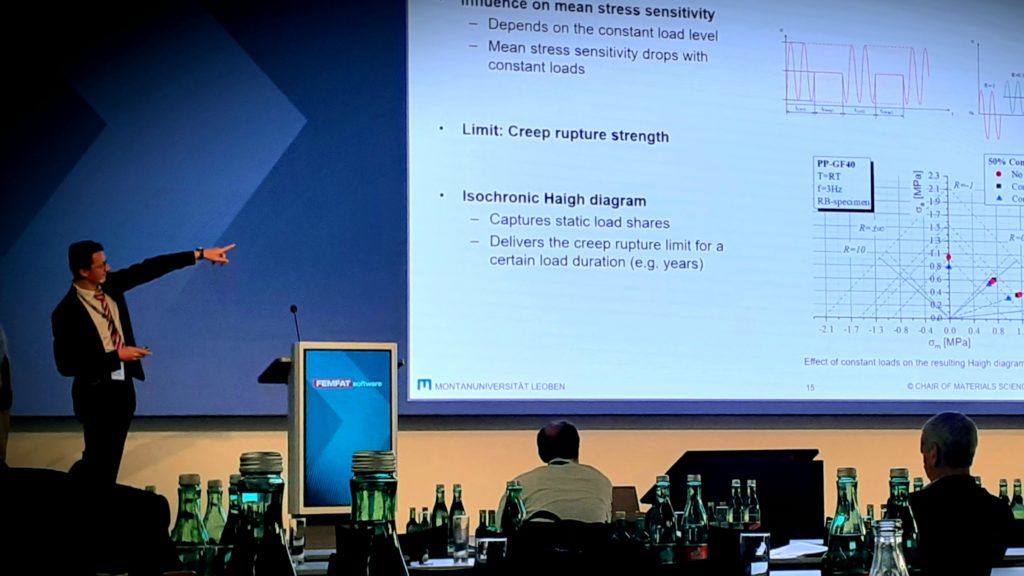
One presentation that caught the attention of many attendees was by Dr. Gabriel Stadler from Montanuniversität Leoben, who discussed the Influence of creep load on the lifetime of short fiber reinforced polymers. As lightweight materials, short fiber reinforced polymers are becoming increasingly important in structural applications, particularly in the automotive sector.
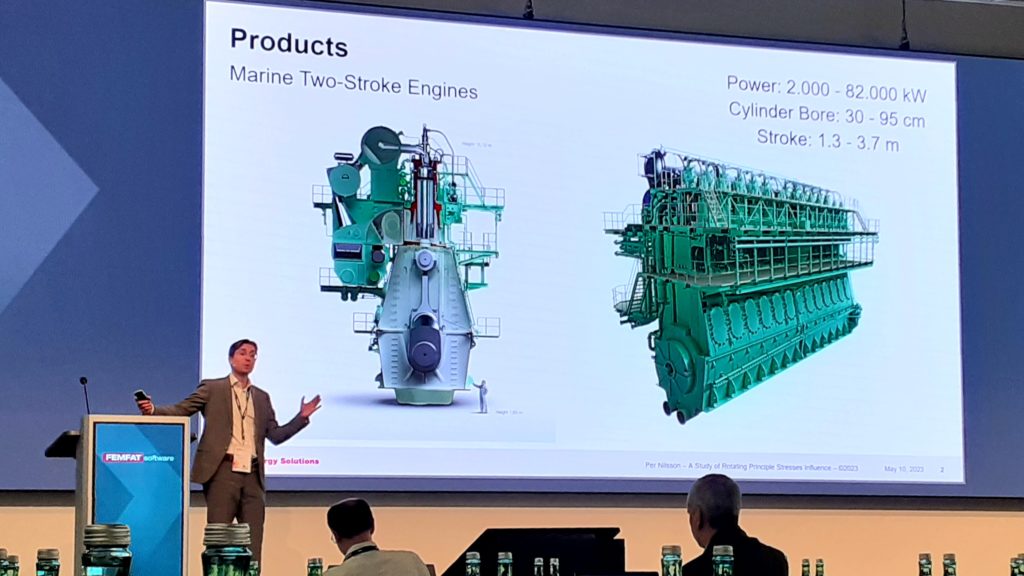
Another noteworthy presentation was by Per Nilsson from MAN Energy Solutions in Denmark, a ship engine manufacturer. His study focused on the FEMFAT Rotating Principle Stresses (RPS) Influence, a functionality that takes multiaxial effects into consideration. The study analyzed the influence of loading parameters such as phase, mean stress, and wave form and how they interact, with particular importance to the ship engine industry where the effect of multi axial stress is critical.
The conference also coincided with Mr. Per Nilsson’s birthday, which was celebrated with a roomful of attendees singing “Happy Birthday” to him. Additionally, there were two FEMFAT workshops during the conference that allowed participants to see the software in practice, making the conference a valuable experience for all who attended. The ECS Simulation Conference was a great opportunity for experts in the field to come together and share their insights, leading to advancements and progress in the world of simulation.
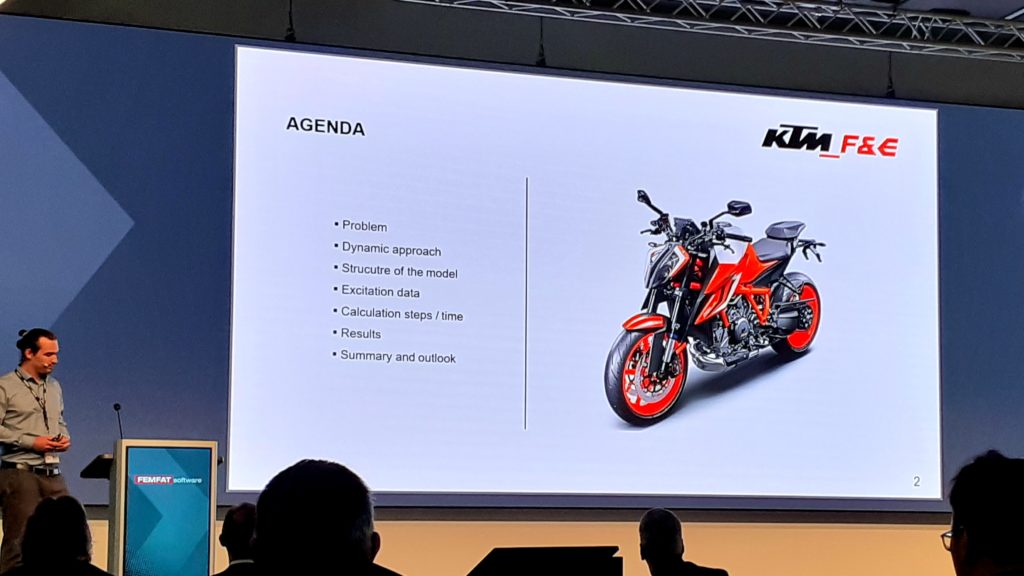
The day continued with a refreshing coffee break and then we delved into a presentation by Lukas Stenzel, a master’s student at KTM, about the method study for fatigue life evaluation of engine attachment points on the main frame of a motorcycle. His work highlighted a comparison of methods for the fatigue life evaluation of engine housings concerning the internal engine loads.
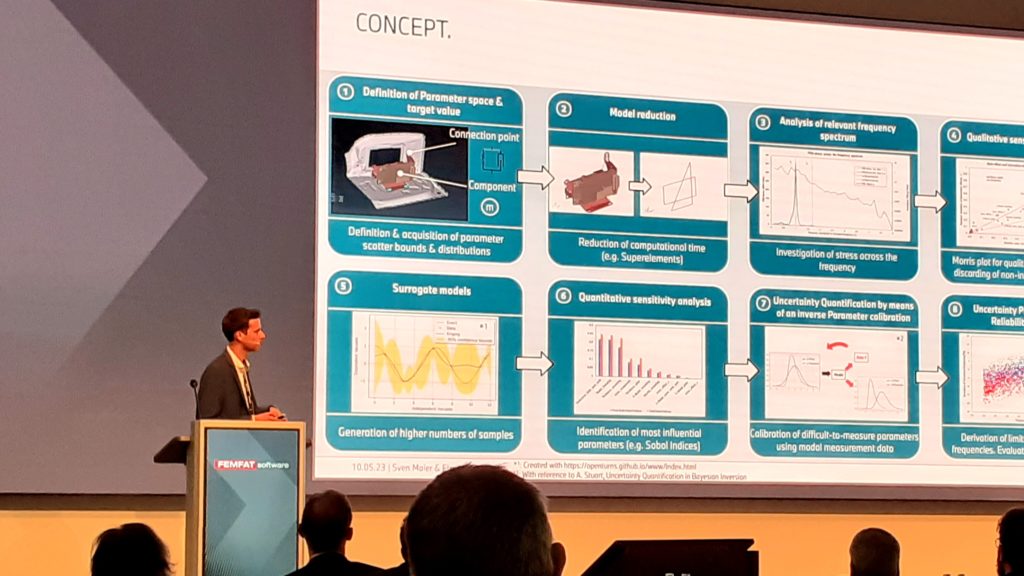
Following that, Sven Maier from BMW presented a concept study on scattering input parameters in structural durability simulations applied to automotive components subjected to vibration loads. The presentation shed light on the numerous subsystems in modern vehicles that are mounted to the body-in-white structure for comfort, safety, digitalization, electrification, and autonomous driving functions. The study revealed that the vibration fatigue behavior of the subsystems and their connection to the body were significant factors, and the damping, mass, and thickness of the mounted component played a vital role in the vibration behavior of the system.
Furthermore, the thicknesses of the plates had a substantial impact on the system’s natural frequencies, and a correlation between natural frequencies and calculated damage was derived.
The ECS Simulation Conference was an exciting event for automotive engineers and simulation experts. The conference was held at the Linz Stahlhaus, and the presentations were informative and insightful.
One of the standout talks was given by Markus Breitfuss, a colleague of mine from Magna Powertrain Engineering Center Steyr. His talk focused on the simulation-based fatigue assessment of car body structures. This topic is crucial for achieving the durability, lightweight, and cost targets in modern vehicle development processes.
Markus explained the concept of inertia relief and dynamic contact analysis. These concepts are two essential processes used in simulation-based fatigue assessment. He also discussed how these processes complement each other and provide accurate and reliable results. The conference continues till next day with more talks and workshops but unfortunately I don’t have the chance to be there! You can also the check the ECS conference website for the full details of the presented Articles and more!
However, todays talks were informative and thought-provoking, leaving the audience with new ideas and concepts to consider. As the presentations for the day concluded, I left the Linz Stahlhaus feeling inspired and excited about the future of simulation and automotive engineering. The ECS Simulation Conference was a great opportunity to learn from experts in the field.