In this project we have investigated the stress distribution in a system of diffuser support legs which was used in the Annealing unit of a galvanized steel company. Some of the supporting legs failed duo to high temperature and loadings and we have analyzed several scenarios for optimizing the design of these supporting legs.
Finite Element Modeling
The Finite Element code which is selected for this work is the ANSYS 18.2. The model is created in metric dimensions and all external loads in Newton (N) to have stresses in Pascal (Pa). Fig. 1 is geometry model and Fig. 3 is finite element model for analysis.
The mesh system of the model is shown in Fig. 2. To increase the accuracy of finite element results, all of the elements types of model have been considered as solid.
The number of elements used for FE model is about 65000 elements with 150,000 degrees of freedom, which represents a good accuracy. At first a thermal analysis has been done and then mechanical loads applied to the FE model to determine stress and deformation distribution in the model.
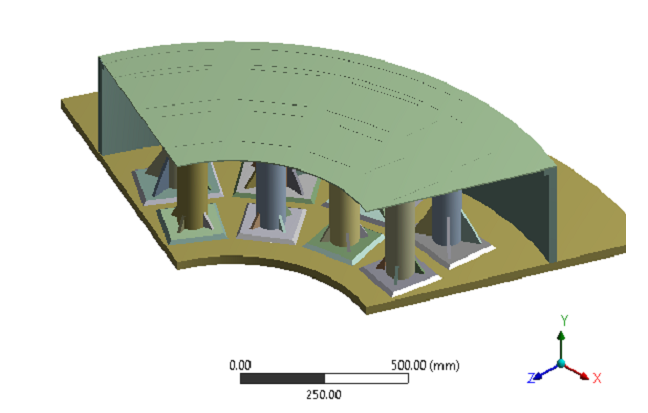
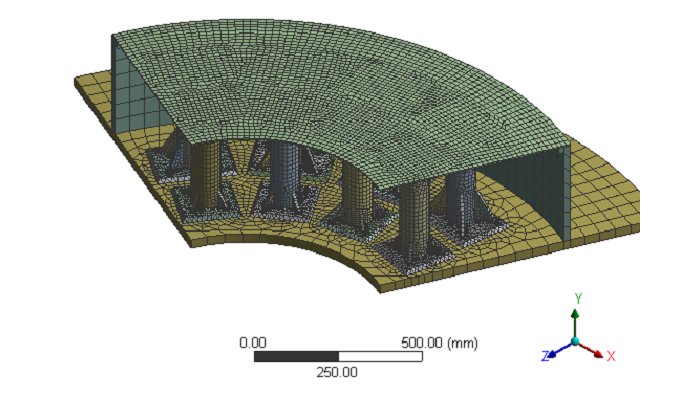
After applying the mechanical loadings, the analysis has performed. Following figure shows the stress contours of supports structure under the design conditions.
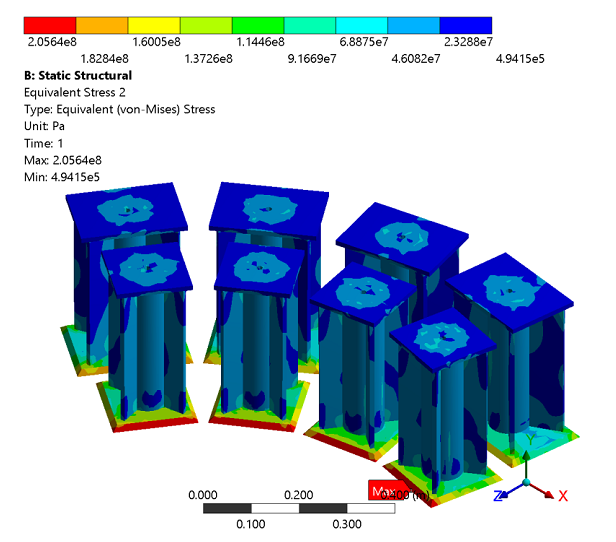
Due date: February 2018